Facilities
The Future LiME Hub, continues to focus on developing fundamental understanding of solidification, and modern, revolutionary techniques and advanced devices for metals processing. Meeting the demands of our industrial partners, the Hub continues to deliver more efficient, less expensive technological solutions for large scale metals production.
The Hub brings together the impressive facilities for solidification research at Brunel University London and our four spokes at the University of Manchester, University of Leeds, University of Oxford and Imperial College London, including: state of the art analytical modelling and molecular dynamic simulation; a range of innovative casting processes; technologies for the engineering and assessment of liquid metals; and an extensive suite of tools for microstructural characterization.
To view our industrial capabilities please download our leaflet.
BCAST promotional video can be found here.
Hub fundamental facilities
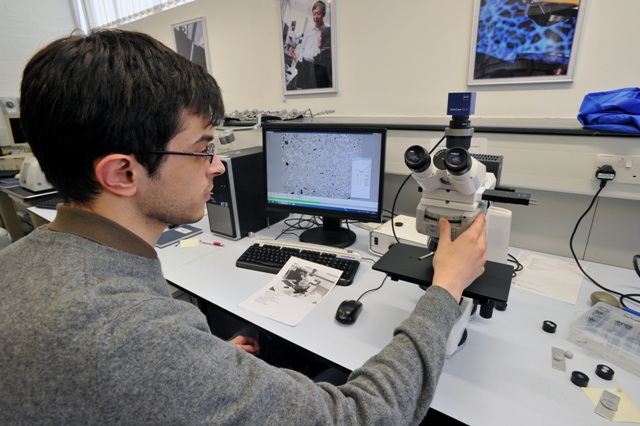
Some highlights:
• Pilot and industrial scale casting facilities including high pressure die casting, low pressure die casting, direct-chill casting, twin roll casting, squeeze casting, investment casting and spray forming.
• Intensive melt shearing and ultrasonic technologies for enhanced nucleation and grain refinement.
• Small scale extrusion and rolling facilities for downstream thermomechanical processing.
• A range of techniques for the control and measurement of the quality of molten alloys including optical emission spectroscopy, rotary degassing, hydrogen measurement, reduced pressure testing and pressurised filtration.
The Fundamental characterisation facilities include:
Small scale casting:
• 450 tonne high pressure die casting machine
• Direct chill casting set up that cast 80 mm direct chill cast billets
• Low force melt conditioned twin roll casting set ups for Al and Mg
• Small scale ingot and permanent mould casting facilities
• Liquidus and density measurement
Compositional analysis:
• Spark emission spectroscopy for composition analysis of standard alloys
• Spectro Blu-ICP-OES spectrometer for the accurate measurement of alloy compositions
Thermal analysis:
• Hot disk TPS 500 thermal constants analyser, which rapidly and accurately measures the thermal conductivity, thermal diffusivity and specific heat capacity
• MAM1 arc melting and suction casting unit used for the preparation of non-ferrous and ferrous alloy casting rods of 30mm in length and diameters ranging from 1mm to 5mm
• Carbolite laboratory tube furnace and elite thermal system laboratory elite thermal box furnace with an operating temperature of up to 1200C for heat treatment of alloys
• Differential Scanning Calorimetry (DSC) with high sensitivity sensors that can operate up to 1150C and maximum heating/cooling rates of 50K/min for the study of heat flow of specimen upon heating, with cooling cycles to determine the thermodynamic properties of metals and the kinetics of phase transformation
Heat treatment facilities:
• Large scale electrical ovens for both solution and heat treatment
• Oil baths to allow constant temperature ageing heat treatments
• Semi automatic medium laboratory vacuum furnace with an operating temperature of up to 2000C and graphite hot zone of 102mm diameter and 51mm high used for heat treatment under either high vacuum at a base pressure of 1×10-5 mB or a dynamic flow of inert gas, such as Argon
Mechanical property analysis facilities:
• Instron mechanical testing set up with elevated temperature capabilities up to 300oC
• Brinell and Vickers hardness testing set ups
• Creep deformation testing
Microstructural characterisation:
• Stereo microscopy to measure fracture surfaces and high depth of field examinations
• Standard reflected light optical microscopy with Ziess Zen analytical software
• Two desktop scanning electron microscopes (SEM) with energy dispersive x-ray spectroscopy (EDS) capabilities capabilities for low magnification fast characterisation
• Access to Zeiss Leo SEM with EDS
• Zeiss AURIGA Crossbeam FIB-SEM with EDS and EBSD capabilities to measure composition as well as texture evolution
• Access Zeiss Supra FEG SEM with EDS and EBSD capabilities to measure composition as well as texture evolution
• Access to Jeol 2100 FEG transmission electron microscope with EDS and EELs capabilities
An overview of the computational facilities can be found here: VEC – web – computational resources
An overview of the CT facilities can be found here: CT capabilities
For more information on the Hub’s facilities please contact Dr Mark Jones on mark.jones@brunel.ac.uk or 01895 268880.
AMCC and AMPC
With £17.4 million of support from the EPSRC, Brunel University London and industry, we opened the Advanced Metals Casting Centre (AMCC) on Brunel’s campus in Uxbridge in April 2016. Housing pilot and commercial metals processing equipment in a 1,500 m2 purpose-built building, the AMCC acts as a national scale-up facility to bridge the gap between fundamental, laboratory-scale research and full-scale industrial trials.
The Advanced Metal Processing Centre (a further 1500 m2) houses additional equipment further expanding our capability in the application of new technology to full scale industrial evaluation. The AMPC contains advanced joining, measurement and characterisation technology.
In support of its industrial partners – Jaguar Land Rover, Constellium and a number of companies in the supply chain – the AMCC will initially serve the automotive industry, but the longer term aim is to make the facilities available to partners in the aerospace and other engineering sectors. Industrial partners will continue to work with the Future LiME Hub for long term basic research, and then through the AMCC/AMPC to scale laboratory developed technologies up to the production demonstrator scale thus shortening the time to bring laboratory discoveries to market.
This is important as technologies often do not progress across the so-called “valley of death” between fundamental research and industrial application. Our facility enables a gated process of evaluation across Technology Readiness Levels (TRL’s). This risk managed process allows only scale-optimised and understood technologies to reach industrial manufacturing processes.
The major equipment installation comprises:
Casting Capability
• 1600 tonne vacuum assisted HPDC
• 600kg aluminium dosing furnace
• 500kg magnesium dosing furnace
• 24 tonne LPDC machine
• Gravity die casting system
• Sand casting line
• Direct Chill casting unit capable casting billets with 205 mm diameter and 2m length
• 1 TRC units for Mg thin strip
Processing Capability
• 350 tonne extrusion press
• 1600 tonne extrusion line
• 3D Freeform bending machine
• Cold Metal Transfer Welding
• Electro-magnetic pulse forming-welding machine
• Micro and Macro CT Scanning Equipment
• GOM Metrology System
• Heat treatment furnaces
• Machining facilities: CNC, CMM
To view information on the individual equipment please view the AMCC equipment page and the AMPC equipment page.
For more information on the Hub’s facilities please contact Dr Mark Jones on mark.jones@brunel.ac.uk or +44 (0)1895 268 880.
Spoke Facilities
Imperial College London
Casting and Crystal Growth Facilities:
– Arc melting, induction melting, resistance melting
– Directional Solidification (Bridgman growth to 1800°C)
Materials Characterisation:
– Electron Microscopy (SEM and TEM) including SEM based EBSD and EDX
– Ion-beam Microscopy (FIB-SIMS, tof-SIMS LEIS, and FIB-SEM tomography)
– Thermal Analysis (DSC, dilatometry, and cooling curve analysis)
– Synchrotron radiography based at SPring-8, Japan.
Within the Imperial spoke there is a focus on the development of computational tools for experimental data analysis including: EBSD datasets, synchrotron radiograph sequences, and tomography datasets.
For more information on Imperial College London’s facilities please contact Dr Chris Gourlay on c.gourlay@imperial.ac.uk or +44 (0) 20 7594 8707.
University of Leeds
Information on the Leeds HPC facility can be found here.
University of Oxford
Casting facilities:
– Small sample furnaces including arc melting, induction and resistance
– Vacuum furnaces up to 1200 °C
In-situ solidification rigs:
– Directional and isothermal solidification rigs for in-situ synchrotron X-ray imaging studies of metal up to 1400 °C
Materials characterization:
– Electron Microscopy – David Cockayne Centre for Electron Microscopy (http://www-em.materials.ox.ac.uk/)
– Atom probe tomography;
– X-ray tomography;
– Oxford Materials Characterization Service (OMCS) (https://www-omcs.materials.ox.ac.uk/)
University of Manchester
Electron Microscopy Centre:
The Electron Microscopy Centre houses a suite of 22 electron microscopes, comprising 13 scanning electron microscopes, 4 dual beam focused ion beam microscopes (including one plasma focused ion beam) and 5 transmission electron microscopes.
– FEI Titan G2 80-200: Is a probe aberration corrected TEM suited for atomic resolution imaging. It can be operated with a range of in-situ holders including gas environmental cell, liquid heating/electrochemistry and heating/ electrical holders.
– FEI Helios Plasma FIB: The dual beam system incorporates a PFIB column and a SEM. The ion column has a high current (1.3 μA) ion source for fast milling and the FEG-SEM for high resolution imaging.
Henry Moseley X-ray Imaging Facility:The X-ray instruments cover a range of image resolutions from 20 nanometres to 1 millimetre for specimens ranging from 60 microns to 1 metre in diameter and length. At Manchester we are the forefront of developing new techniques in 3D imaging and we host one of the most extensive X-ray computed tomography (CT) imaging facilities in the world. This allows our team to collect 3D images for precise analysis.
– Zeiss Xradia Versa 520 with DCT: The Versa DCT is a sub-micron resolution scanner that utilises Diffraction Contrast Tomography (DCT). DCT allows for the identification of the crystallography of grains within polycrystalline materials by obtaining diffraction patterns during the tomography scan. Thus, quantitative crystallographic information of the grains can be obtained in 3D.
– Zeiss Xradia Ultra 810: The Ultra is the highest resolution lab-based X-ray tomography system that is commercially available. The system permits imaging at nanometre scale by using state-of-the-art zone plate X-ray optics to achieve resolutions as fine as 50 nm.